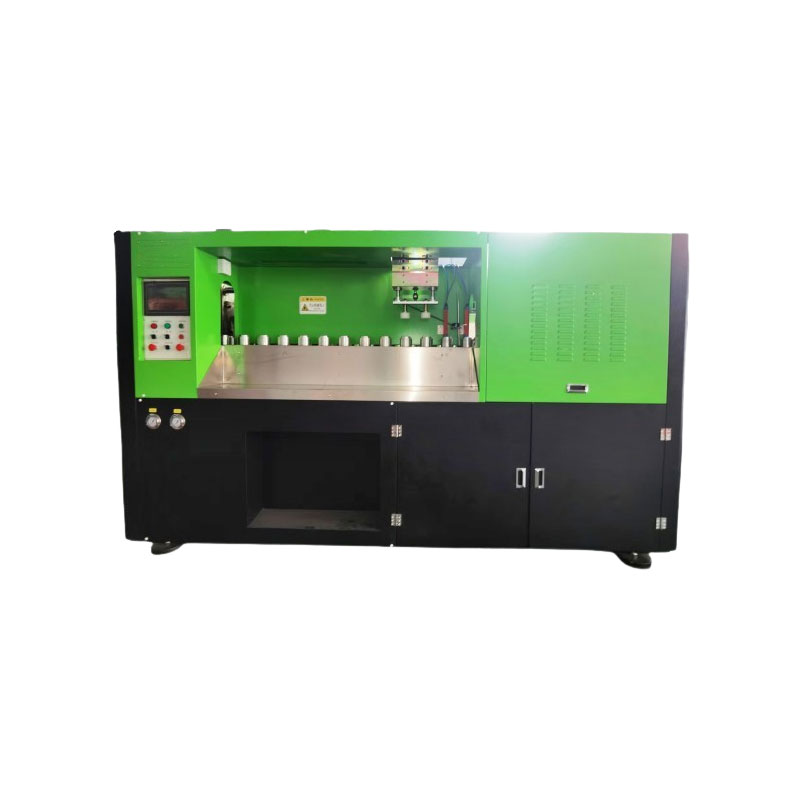
Blowing Machine for Plastic Bottle
- Product Information
Blowing Machine for Plastic Bottle is a core product developed by BOHANG, which is specially designed for efficient and precise plastic bottle Molding process. The equipment adopts modular design and is compatible with a variety of materials such as PET, PP, PE, etc. It can produce various bottle types from 50ml to 5L. The machine is equipped with an intelligent control system to achieve full-process automated production, while supporting personalized customization services to meet the production capacity, precision of different customers. BOHANG provides one-stop plastic bottle molding solutions for global customers with excellent technology and reliable quality.
Blowing Machine for Plastic Bottle Features:
1. High efficiency and energy saving:
Blowing Machine for Plastic Bottle adopts servo drive system and dynamic energy-saving technology, and its energy consumption is reduced by 30% compared with traditional models. The independent temperature control system accurately adjusts the heating power to avoid energy waste; the optimized design of the hydraulic system reduces ineffective work, and a single device can save hundreds of yuan in electricity bills per day, helping enterprises to achieve green production.
2. High-precision molding:
Blowing Machine for Plastic Bottle is equipped with a closed-loop pressure control system and precision mold positioning technology, and the uniformity error of the bottle wall thickness is ≤0.1mm, ensuring that the product qualification rate exceeds 99.5%. The intelligent visual inspection module monitors key dimensions such as bottle mouth and thread in real time, and automatically removes defective products to meet the stringent quality requirements of the high-end market.
3. Fast mold change:
The modular mold design supports bottle type switching within 10 minutes, and can be disassembled and installed without complex tools. The pre-adjusted parameter library can store 50 sets of process data, and production can be resumed with one-click call, which significantly shortens the order conversion time and improves flexible production capacity.
4. Stable and durable:
The core components are made of imported alloy steel and heat treatment process, and the life of key bearings exceeds 50,000 hours. The fully enclosed lubrication system reduces oil pollution, and cooperates with the automatic cleaning program to ensure that the equipment maintains a low failure rate in 24-hour continuous operation, and the maintenance cost is reduced by 40%.
5. Safety protection:
The Blowing Machine for Plastic Bottle is equipped with a three-level safety protection system: emergency stop button, infrared grating and access control interlock device to ensure the safety of operators. The pressure sensor monitors the hydraulic system in real time and automatically releases pressure when overpressure; the exhaust gas outlet is equipped with a filter device, which meets the EU CE safety standards.
6. Silent design:
The low-noise fan and soundproof cover structure are adopted, and the equipment operating noise is ≤75dB, which is better than the industry average. The shock-absorbing base and flexible transmission system further reduce vibration, improve the workshop working environment, and meet the comfort needs of modern factories.
7. Environmental protection and compatibility:
Support PET recycled material processing and help enterprises achieve circular economy goals. The waste recycling system automatically collects scraps and crushes them for reuse, reducing the waste of raw materials; the cooling water circulation system reduces water consumption, which is in line with the global trend of sustainable development.
Blowing Machine for Plastic Bottle Application:
1. Food and Beverage Industry
Provide customized bottle solutions for mineral water, carbonated beverages, juice and other companies, supporting special-shaped bottles and lightweight bottle designs. The pressure test module ensures that the container meets FDA food-grade standards and meets aseptic filling requirements.
2. Daily Chemical Products
Applicable to high-viscosity liquid packaging such as shampoo, shower gel, and hand sanitizer. The equipment is compatible with wide-mouth bottles and pump-head bottles, and the mold surface treatment technology prevents bottle scratches and enhances the shelf appeal of the product.
3. Pharmaceutical Packaging Market
Produce GMP-compliant medicine bottles and eye drop bottles for pharmaceutical companies. The fully enclosed production environment and oil-free lubrication system avoid contamination, and the UV disinfection module can be integrated into the production line to ensure the safety of medical supplies.
4. Chemical Industry Application
Corrosion-resistant coating technology enables the equipment to handle chemical raw material packaging containing acid and alkali components. The explosion-proof motor and static elimination device meet the production specifications of hazardous goods and support the stable molding of hollow containers below 5L.
5. Agriculture and Pet Products
Provide customized services for pesticide bottles, fertilizer tanks and pet food packaging. Thick-wall molding technology enhances the container's pressure resistance, and the anti-permeability coating extends the product's shelf life and adapts to harsh outdoor storage environments.
Blowing Machine for Plastic Bottle Maintenance:
1. Daily cleaning
After daily shutdown, use compressed air to clean the heating plate, mold surface and conveyor belt residue to avoid adhesion of thermoplastic materials. The cooling water tank needs to be emptied and flushed with scale every week to prevent clogging of the circulation pipe.
2. Lubrication management
Add special high-temperature grease every 500 hours according to the lubrication points marked in the equipment manual. The hydraulic oil needs to be tested for acid value every 2000 hours, and replaced immediately when it exceeds 0.5mgKOH/g to prevent oil oxidation and corrosion of seals.
3. Electrical system inspection
Tighten the wiring terminals once a month to prevent loosening caused by vibration. Use an infrared thermometer to monitor the temperature of components such as inverters and contactors. Abnormal temperature rise (>80℃) requires checking load or heat dissipation problems.
4. Mold maintenance
Disassemble the mold after every 100,000 productions, and repair the wear on the parting surface with diamond grinding paste. After the cavity surface is coated with rust inhibitor, it is sealed and stored to avoid oxidation caused by a humid environment.
5. Pneumatic system maintenance
Drain the condensed water from the air tank every week and check the oil level of the triple lubricator. When replacing the filter element, the sealing ring must be replaced simultaneously to prevent compressed air leakage from affecting the stability of the blowing pressure.
6. Safety device test
Simulate emergency stop button and grating failure every quarter to verify the effectiveness of the safety circuit. The pressure gauge and temperature sensor need to be calibrated once a year to ensure the accuracy of the control system data and avoid misjudgment leading to production accidents.